When it comes to producing precision metal parts, Aluminum Die Casting and Zinc Die Casting are two of the most trusted methods used across various industries. Both processes involve injecting molten metal into a steel mold or die under high pressure to create intricate and dimensionally accurate components. However, the performance, properties, and cost-efficiency of aluminum and zinc differ significantly.
Understanding the differences between aluminum and zinc die casting is critical when choosing the right material and process for your product design and industrial needs. In this article, we break down the key differences to help you make an informed decision.
Material Characteristics: Aluminum vs Zinc
Aluminum Die Casting uses lightweight aluminum alloys that are ideal for high-strength applications where weight reduction is essential. These alloys are commonly used in the automotive, aerospace, and electronics industries due to their high corrosion resistance and excellent thermal conductivity.
Zinc Die Casting, on the other hand, utilizes zinc alloys such as Zamak 3 and Zamak 5. Zinc is known for its superior dimensional accuracy, toughness, and the ability to create highly detailed components. Zinc Die Casting Manufacturers in India often prefer zinc for smaller, more intricate parts used in electronics, home hardware, and industrial components.
Weight and Strength
One of the most noticeable differences between these two materials is their weight.
- Aluminum is significantly lighter than zinc, making it the preferred choice for components in transportation industries where reducing weight improves fuel efficiency and overall performance.
- Zinc, while heavier, offers greater toughness and ductility, making it ideal for products that require impact resistance and fine detailing.
In terms of strength, both materials perform well, but in different ways. Aluminum offers excellent tensile strength, especially at higher temperatures. Zinc offers high impact strength and is more malleable, which helps in complex molding and reduces the risk of cracking during casting.
Precision and Surface Finish
Zinc Die Casting excels in producing parts with tight tolerances, thin walls, and fine details. The lower melting point of zinc (~420°C) allows for better flow into intricate mold designs, resulting in less need for secondary machining.
Aluminum Die Casting also produces precise components, but it may require additional post-processing to achieve the same level of detail and surface finish as zinc. This makes zinc more suitable for components where finish quality and dimensional precision are top priorities.
Corrosion and Heat Resistance
Aluminum is naturally resistant to corrosion due to the formation of an oxide layer on its surface. This makes Aluminum Die Casting ideal for outdoor or marine applications, as well as for parts that need to withstand high-temperature environments.
Zinc also provides good corrosion resistance, especially when coated or plated. However, zinc has a lower melting point, which limits its application in high-heat conditions compared to aluminum.
Cost Efficiency and Tool Life
Cost is often a determining factor in material choice. While Aluminum Die Casting offers performance advantages in certain applications, it typically requires higher energy consumption and shorter tool life due to the elevated temperatures used in the process.
In contrast, Zinc Die Casting offers longer die life, faster cycle times, and lower overall production costs, making it a preferred option for high-volume manufacturing.
Ideal Applications
Aluminum Die Casting is commonly used for:
- Automotive engine components
- Aerospace parts
- Electronic enclosures
- Structural housings
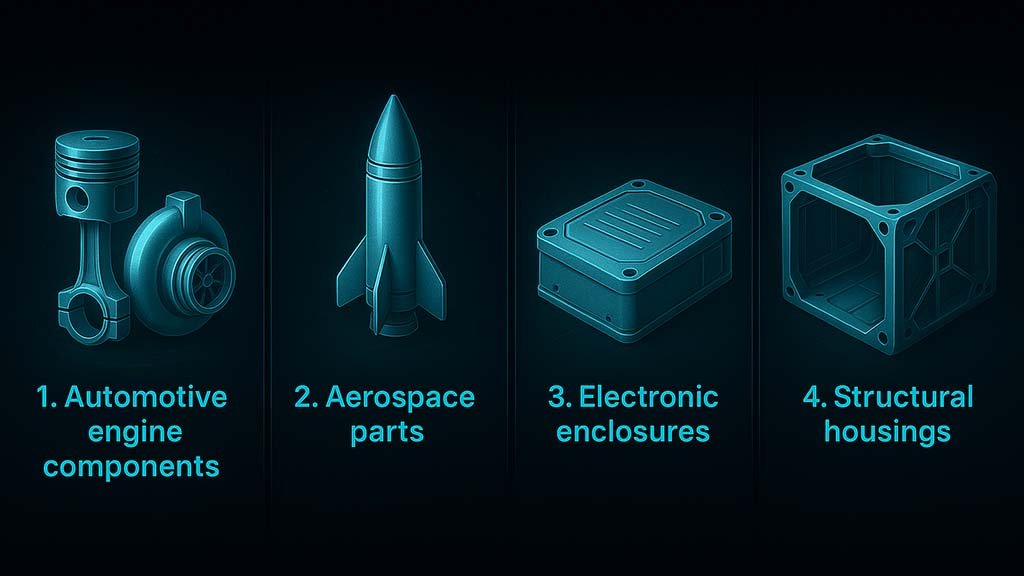
Zinc Die Casting is ideal for:
- Precision gears and connectors
- Decorative hardware
- Small electrical components
- Consumer and industrial fittings
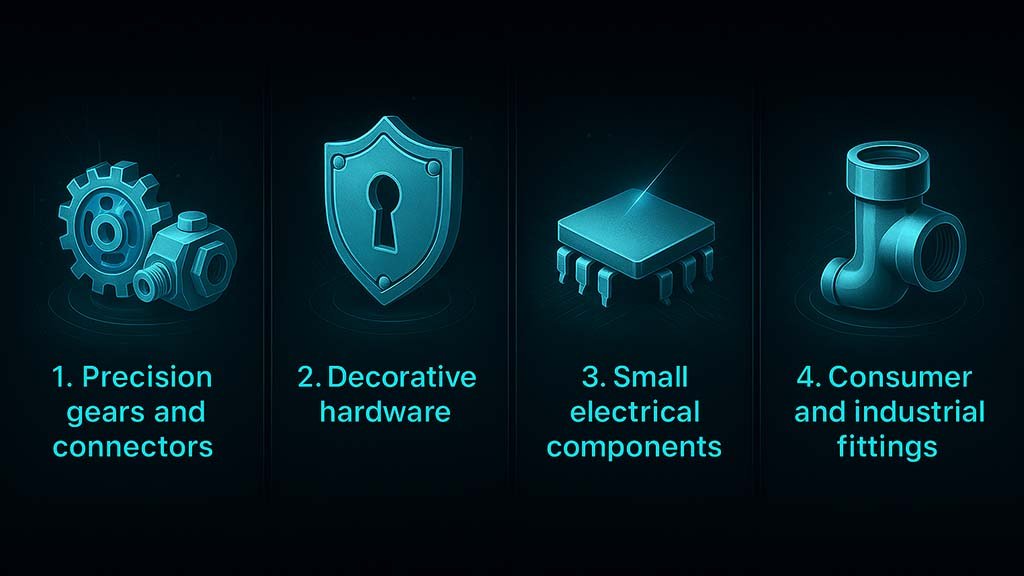
Conclusion
Both Aluminum Die Casting and Zinc Die Casting offer unique advantages that suit different industrial needs. When evaluating which to choose, consider factors such as part size, mechanical requirements, production volume, and budget.
For intricate, small, and cost-efficient parts, Zinc Die Casting is the way to go—especially when working with leading Zinc Die Casting Manufacturers in India. For lightweight, high-strength, and heat-resistant components, Aluminum Die Casting is the superior option.
Looking for a trusted partner for your casting needs? OME Verma Industries, a Leading Aluminium Die Casting Manufacturer in India, delivers high-quality solutions with precision engineering, advanced technology, and industry-proven expertise.